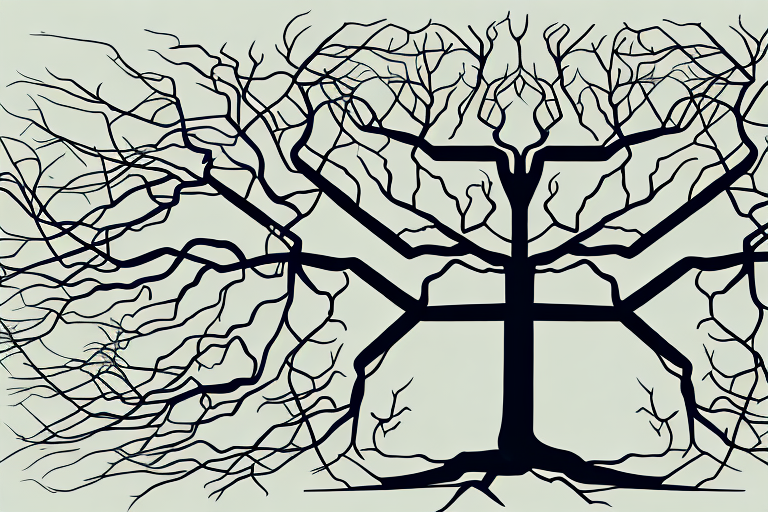
Discover the power of the 5 Whys technique in problem-solving.
The 5 Whys technique is a powerful method that allows individuals and organizations to delve deep into the root causes of problems. By continuously asking "Why?" five times, one can peel away the layers of symptoms to uncover the core issue. This article explores the concept, significance, practical steps for implementation, and its applications across various industries, alongside its limitations.
The 5 Whys is a simple yet effective problem-solving tool developed by Sakichi Toyoda and is part of the Toyota Production System. This technique encourages teams to explore the cause-and-effect relationships underlying particular problems. By identifying the root cause rather than just addressing superficial symptoms, businesses can implement more effective and long-lasting solutions.
The 5 Whys technique originated in the manufacturing industry, specifically within Toyota's efforts to improve quality and efficiency. It was formalized in the 1950s as part of the company's continuous improvement philosophy, known as Kaizen. The method gained popularity because of its straightforward approach and effectiveness in resolving issues without extensive data collection or complex analysis. Over the years, this technique has transcended its manufacturing roots and found applications in various sectors, including healthcare, software development, and service industries, demonstrating its versatility and relevance in contemporary problem-solving.
The basic principle of the 5 Whys is rooted in the idea that asking "Why?" repeatedly will lead one to the core cause of a problem. By collectively brainstorming and discussing potential reasons for an issue, teams can foster a deeper understanding of the situation. This approach not only identifies the root cause but can also reveal interconnected issues that may have gone unnoticed. Importantly, the 5 Whys encourages a culture of open communication and collaboration, as team members are invited to share their insights and perspectives. This collective inquiry not only enhances problem-solving capabilities but also promotes a sense of ownership and accountability among the team members, ultimately leading to a more engaged workforce.
To effectively implement the 5 Whys, teams should begin by clearly defining the problem at hand. Once the issue is articulated, the team can start the questioning process, asking "Why?" for each answer provided until they reach the root cause. It is essential to document each step of the inquiry to ensure that all perspectives are captured and to facilitate further discussion. Additionally, teams may find it beneficial to involve individuals from different departments or areas of expertise, as this diversity can lead to richer insights and a more comprehensive understanding of the problem. By fostering an environment where questioning is encouraged, organizations can not only solve immediate issues but also build a framework for continuous improvement that can adapt to future challenges.
Root cause analysis is essential for any organization aiming to improve its processes and outcomes. Utilizing the 5 Whys technique provides teams with a framework to dissect problems systematically. This understanding can mitigate risks and enhance operational efficiency. Furthermore, organizations that prioritize root cause analysis often find that it leads to a more engaged workforce, as employees feel their insights and experiences are valued in the decision-making process. This engagement can translate into higher job satisfaction and lower turnover rates, creating a more stable and knowledgeable team.
By employing the 5 Whys technique, teams sharpen their problem-solving skills. Engaging in this systematic inquiry fosters critical thinking and encourages team members to look beyond surface-level issues. Over time, this cultivates a culture of reflective thinking within the organization. Additionally, as team members become more adept at identifying root causes, they can also share their knowledge with new employees, creating a continuous learning environment. This mentorship not only accelerates the onboarding process but also strengthens team cohesion, as members collaborate to solve complex challenges together.
One of the primary advantages of root cause analysis is its capability to prevent the recurrence of issues. By identifying and addressing the underlying causes of problems, organizations are better equipped to implement preventive measures that target these root causes rather than merely treating the symptoms. This proactive approach saves time, resources, and boosts overall productivity. Moreover, organizations that successfully implement root cause analysis often find that it leads to improved customer satisfaction. By resolving issues at their source, companies can deliver higher quality products and services, thereby enhancing their reputation and fostering customer loyalty. This ripple effect can significantly impact the bottom line, as satisfied customers are more likely to return and recommend the business to others.
While the 5 Whys technique is straightforward, following a structured approach enhances its effectiveness. Here are the essential steps to implement this method successfully.
The first step in any problem-solving process is to clearly define the issue at hand. Teams should gather relevant information and ensure consensus on the problem that needs to be addressed. This clarity will guide subsequent questioning. Additionally, it can be beneficial to involve diverse perspectives from team members, as different experiences and insights can illuminate various facets of the problem. This collaborative approach not only fosters a sense of ownership among team members but also enriches the understanding of the issue, setting a solid foundation for the next steps.
The next step is to ask "Why?" regarding the identified problem. This question should generate a response that takes the team a step closer to understanding the cause. It's crucial to ensure that responses are factual and based on observable evidence whenever possible. Encouraging an open dialogue during this phase can lead to more thoughtful and comprehensive answers. Team members should feel comfortable sharing their thoughts without fear of judgment, as this openness can reveal underlying factors that may not be immediately apparent.
After addressing the first “Why,” continue the questioning process, asking "Why?" for each subsequent answer provided. It's essential to document each response, as it helps track the logic leading to the root cause. Typically, this process will require at least five "Whys," but some issues may need more or less probing. As the team delves deeper, they may uncover systemic issues or recurring patterns that contribute to the problem. This stage is crucial, as it not only identifies the root cause but also highlights potential areas for improvement, allowing the team to think critically about solutions that address the problem at its source rather than merely treating symptoms.
The versatility of the 5 Whys technique allows it to be applied across various sectors, each with distinct challenges and problem-solving needs. Let’s explore how it plays a role in different industries.
In the manufacturing sector, the 5 Whys technique can be particularly impactful. It helps identify equipment failures, quality control issues, and process inefficiencies. By addressing these root causes, companies can avoid costly downtime and enhance production quality. For instance, if a machine breaks down, the team can ask why it failed, leading them through a series of inquiries that might uncover inadequate maintenance schedules or even operator training gaps. This method not only resolves the immediate issue but also fosters a culture of continuous improvement, encouraging employees to think critically about processes and outcomes.
In healthcare, applying the 5 Whys can reveal underlying issues contributing to medical errors or inefficiencies in patient care. By understanding why these errors occurred, healthcare providers can ensure better patient safety and establish protocols that prevent recurrence. For example, if a patient receives the wrong medication, the investigation might uncover a breakdown in communication between staff or flaws in the electronic health record system. By addressing these root causes, healthcare organizations can enhance their operational protocols and training programs, ultimately leading to improved patient outcomes and trust in the healthcare system.
In IT services, the 5 Whys technique can assist in diagnosing system failures or service interruptions. By investigating the root causes of these issues, IT teams can implement more effective solutions, thereby minimizing future outages and enhancing service reliability. For instance, if a server crashes, the team might discover that the initial cause was a software bug, which leads to further inquiries about why the bug was not caught during testing. This process can reveal gaps in the quality assurance protocols or the need for better collaboration between development and operations teams. By systematically addressing these issues, organizations can not only resolve the immediate technical problems but also strengthen their overall IT infrastructure.
Despite its advantages, the 5 Whys technique is not without its limitations. Understanding these criticisms is vital for effective implementation.
One of the common criticisms of the 5 Whys technique is that it can lead to oversimplification of complex problems. While it is effective for straightforward issues, more complex scenarios may require a broader range of analytical tools to uncover the multifaceted causes.
Related to oversimplification is the inherent risk of subjectivity in responses. Each team member's perspective may skew interpretations of the problem's causes. Therefore, it is crucial to base discussions on facts and data to minimize biases.
As organizations continue to navigate complex challenges, the 5 Whys method remains a vital tool in the problem-solving arsenal. By effectively identifying and addressing root causes, businesses can not only correct immediate issues but also enhance overall performance and collaboration.
In the roofing industry, where proper assessments and claims management are essential, firms like Boss Up Solutions exemplify the effective implementation of the 5 Whys approach. Their transparent flat fee pricing for roofing and insurance restoration contractors ensures value when writing estimates and managing claims or supplements, allowing teams to focus on root causes and solutions rather than administrative burdens. By applying the principles highlighted in this article, companies can achieve meaningful improvements in their operations.